Одношпиндельный станок для глубокого сверления с ЧПУ: RAPIRA SGS-01
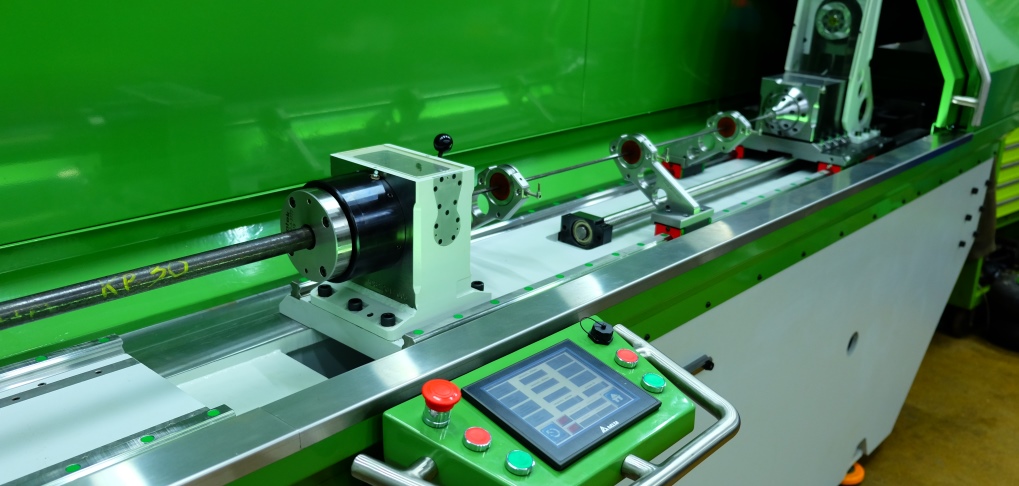
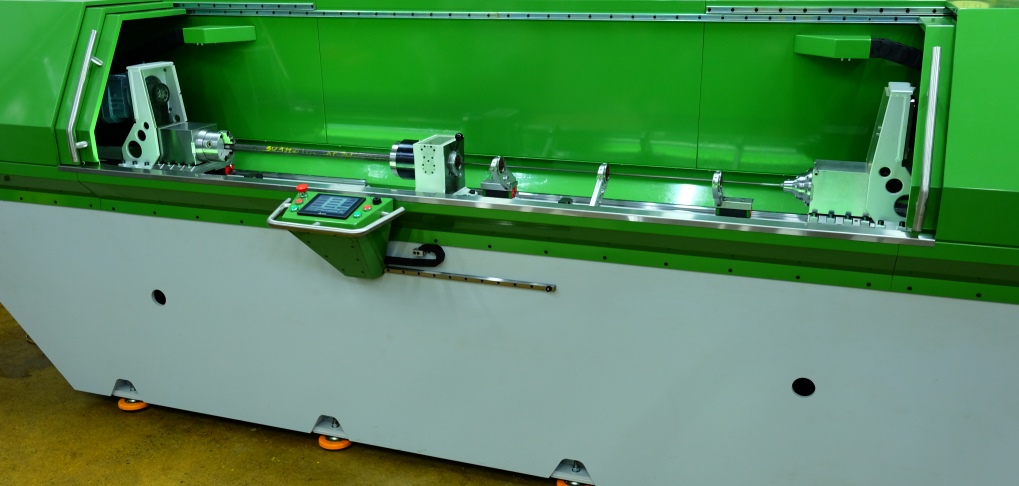
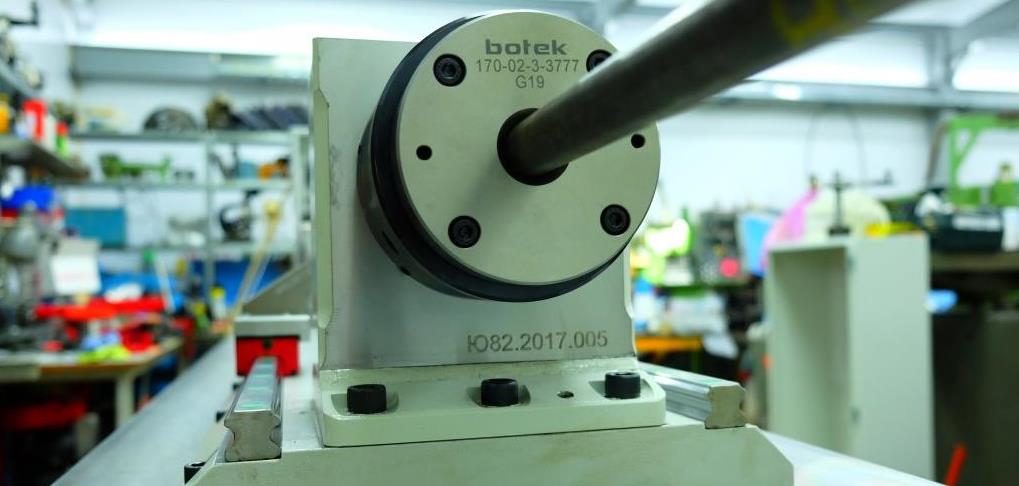
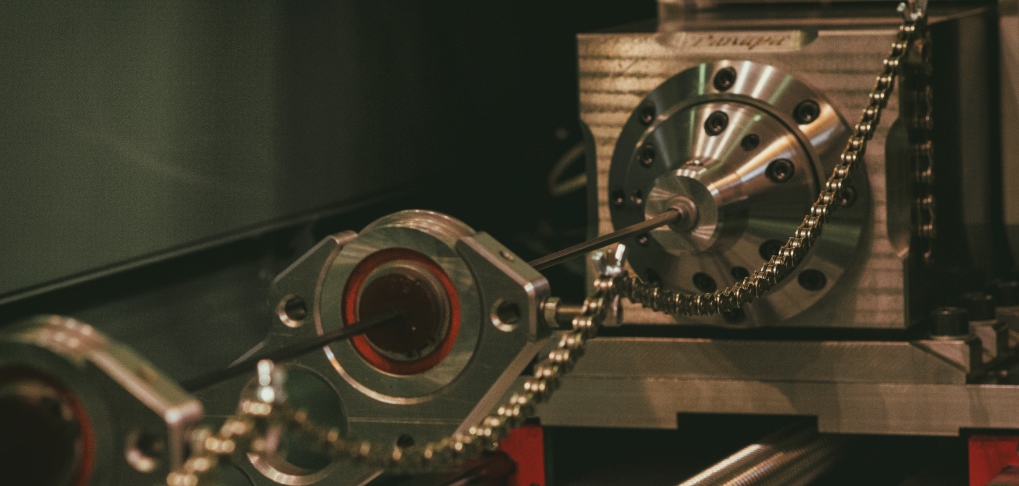
Российский станок для глубокого сверления RAPIRA SGS-01 спроектирован для сверления глубоких отверстий пушечными однолезвийными сверлами (ELB) в цилиндрических заготовках длиной до 1100 мм. RAPIRA SGS-01 является базовой моделью. Станок позволяет серийно обрабатывать детали с наружным диаметром до 60 мм и диаметром сверления до 20 мм.
Увод сверла при диаметре сверления до 14,5 мм — ≤0,02/100 мм.
Увод сверла при диаметре сверления от 14,5 мм — ≤0,03/100 мм.
Станок одношпиндельный.
Станок позволяет обрабатывать конструкционные стали, углеродистые, легированные, нержавеющие, жаропрочные, а также цветные и титановые сплавы твердостью от 15 до 40 по шкале Роквелла (HRC).
Более 75% деталей и узлов станка российского производства.
Смотреть каталог оборудования для глубокого сверления и растачивания
- Станок для глубокого сверления RAPIRA SGS-01
- Система крепления заготовки (Трехкулачковый самоцентрирующий патрон)
- Система поддержки заготовки (люнеты) – 2 шт
- Система поддержки инструмента (буксируемые люнеты) – 3 шт
- Система стружкоудаления (немагнитный ленточный транспортер)
- Система очистки (ленточный фильтр) и подачи СОЖ
- Охладитель СОЖ воздушного типа
- Защитное ограждение (Кабинет)
- Пакет стартовой оснастки (пассивный шпиндель, зажимной конус, люнетная и кондукторная втулки, ружейное сверло)
- Комплект виброопор для установки станка
- Комплект ручных инструментов для обслуживания станка
- СОЖ (Масло) для сверления
- Документация на русском языке (Паспорт, Руководство по эксплуатации, Руководство оператора)
- Увеличение глубины сверления до 1300 мм
- Система для отделения масла от стружки (Центрифуга)
- Система автоматического зажима заготовки (автоматический трехкулачковый патрон и гидравлический люнет)
- Система автоматической загрузки/выгрузки обрабатываемых заготовок
- Чиллер для охлаждения СОЖ
- Система удаления масляных паров из рабочей зоны станка
- Система ЧПУ Siemens Sinumerik 840D sl
- Ружейные (пушечные) сверла для глубокого сверления с оснасткой для обработки диаметров по ТЗ Заказчика
- Станок для заточки ружейных сверл
- Расширенная гарантия до 24-х месяцев
Характеристики оборудования | Ед.изм. | Величина |
Класс точности станка по ГОСТ 8-77 | — | П |
Количество шпинделей | шт | 1 |
Конструкция станка | — | Горизонтальная компоновка, модульный тип, возможность перемещения задней бабки |
Метод обработки отверстий на станке | — | Система ELB (Gundrilling): однокромочное сверление, обработка при вращении заготовки и противоположном вращении инструмента. |
Материал обрабатываемых заготовок | — | Конструкционные стали; углеродистые, легированные, нержавеющие, жаропрочные стали; цветные и титановые сплавы (группы обрабатываемых материалов по ISO: P, M, S, N) |
Условия эксплуатации: — Вид климатического исполнения по ГОСТ 15150-69 — категория размещения изделия по ГОСТ 15150-69 | — | У
4 |
Высота центров над полом | мм | 1130 |
Ход ШУ инструмента: — с установленными люнетами — со снятыми люнетами | мм | 1390 1440 |
Ход ШУ заготовки | мм | 900 |
Максимальная глубина сверления (длина сверления на проход) | мм | 1100 |
Диаметр сверления: — min — max | мм | 4 20 |
Длина обрабатываемых заготовок | мм | 500-1100 |
Наружный диаметр обрабатываемых заготовок | мм | 20-60 |
Увод сверла при диаметре сверления до 14 мм | мм | ≤0,02/100 |
Увод сверла при диаметре сверления от 14 мм | мм | ≤0,03/100 |
Допуск по диаметру | мм | ≤+0,1 |
Мощность привода инструмента | кВт | 3,7 |
Мощность привода обрабатываемой детали | кВт | 3 |
Тип регулирования оборотов привода | бесступенчатый | |
Скорость вращения инструмента | Об/мин | 800-6000 |
Скорость вращения детали (контр вращение) | Об/мин | 20-300 |
Подача инструмента: — рабочая — ускоренная | Мм/мин | 5-100 500 |
Тип линейной передачи | — | Шарико-винтовая пара |
Система крепления обрабатываемой детали | — | Самоцентрирующий патрон, внешний конус |
Система поддержки инструмента | — | Буксируемые люнеты 3 шт. |
Смена инструмента | — | ручная |
Объем СОЖ | л | 1000 |
Насос высокого давления СОЖ | шт | 1 |
Давление СОЖ при подаче в зону резания | бар | До 120 |
Расход СОЖ при подаче в зону резания | л/мин | 60 |
Тип фильтра СОЖ | Ленточный бумажный фильтр 5-10 микрон | |
Производительность фильтра СОЖ | л/мин | 60 |
Система стружкоудаления | Немагнитный ленточный транспортер | |
Панель управления | Siemens | |
Контроллер | Siemens | |
Габаритные размеры, ДхШхВ, без системы очистки и подачи СОЖ | мм | 4750 х 1270 х 1700 |
Масса, ориентировочно | кг | 3350 |